Description
In falling film evaporators, liquid and vapors flow downwards in parallel flow. The liquid to be concentrated is preheated to boiling temperature if required. An even thin film enters the heating tubes via a distribution device in the head of the evaporator, flows downward at boiling temperature, and is partially evaporated.
The liquid to be evaporated is evenly distributed on the inner surface of a Glass tube. The liquid will flow downwards forming a thin film, from which the boiling/evaporation will take place because of the heat applied by the hot oil . . A number of tubes are built together side by side. At each end the tubes are fixed to tube plates, and finally the tube bundle is enclosed by a shell made either of steel or Glass depending upon the Hot oil pressure. The Hot oil is introduced through the shell. The space between the tubes is thus forming the heating section. The inner side of the glass tubes is called the boiling section. The concentrated liquid and the vapour leave the evaporator at the bottom part, enters the subsequent separator tangentially from where the concentrated liquid is discharged (usually by means of the pump) from the bottom and vapor leave the separator from top.
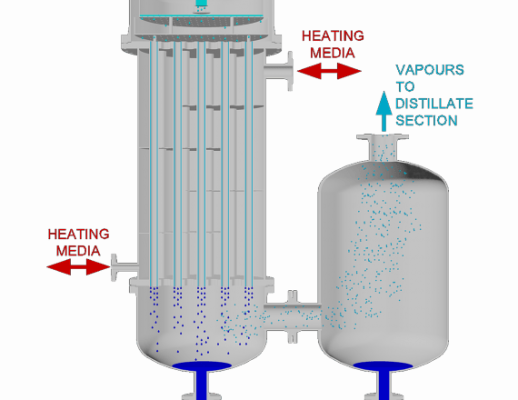
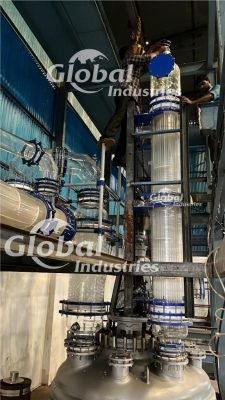
Falling film Evaporator size and available of :
Are available in Heat transfer area from 2 Sq. Mt to 26 Sq. Mt. and from Diameter 4” to 16”. Larger sizes can be offered on request.
Application
- Heat Sensitive products that require careful drying, vaporization like alkaline concentration and flakes production, brine concentration,
- Removal of moisture content from biodiesel
- Detergent and surfactant
- Crop Protection and Bio stimulants
- Recovery of solvents in process industry
- Food and paper industry
- Purification of Bio-diesel
- Evaporation of Solvents
- Concentration of Pharma Products
Falling film Evaporator features
- Highly suitable for heat sensitive products
- Minimizes thermal degradation due to short product contact time
- Fouling is minimized due to low tube wall temperature and heat flux
- The thinner film formation inside the tubes helps in minimizing flooding
- Higher tube side heat transfer coefficient.
- Vacuum Evaporation helps in gentle heating and efficient product removal of best quality.
RELATED CONTENT
This product belongs to the solution